

Important, but less extensive, uses are found in the production of non-ferrous alloys. It is the search for compounds of increased specificity which has stimulated most of the recent work on the coordination chemistry of Tc. Though the circumstances of clinical usage mean that the precise formulation of the compound actually administered is frequently uncertain, † the imaging of brain, heart, lung, bone and tumours etc. A wide range of N-, P- and S-donor ligands has been used to prepare complexes of Tc, mainly in oxidation states III, IV and V, which are absorbed preferentially by different organs. These generators can be made available virtually anywhere and, when required, TcO 4 − is eluted from the substrate and reduced (Sn II is a common, but not the sole, reductant) in the presence of an appropriate ligand, ready for immediate use.
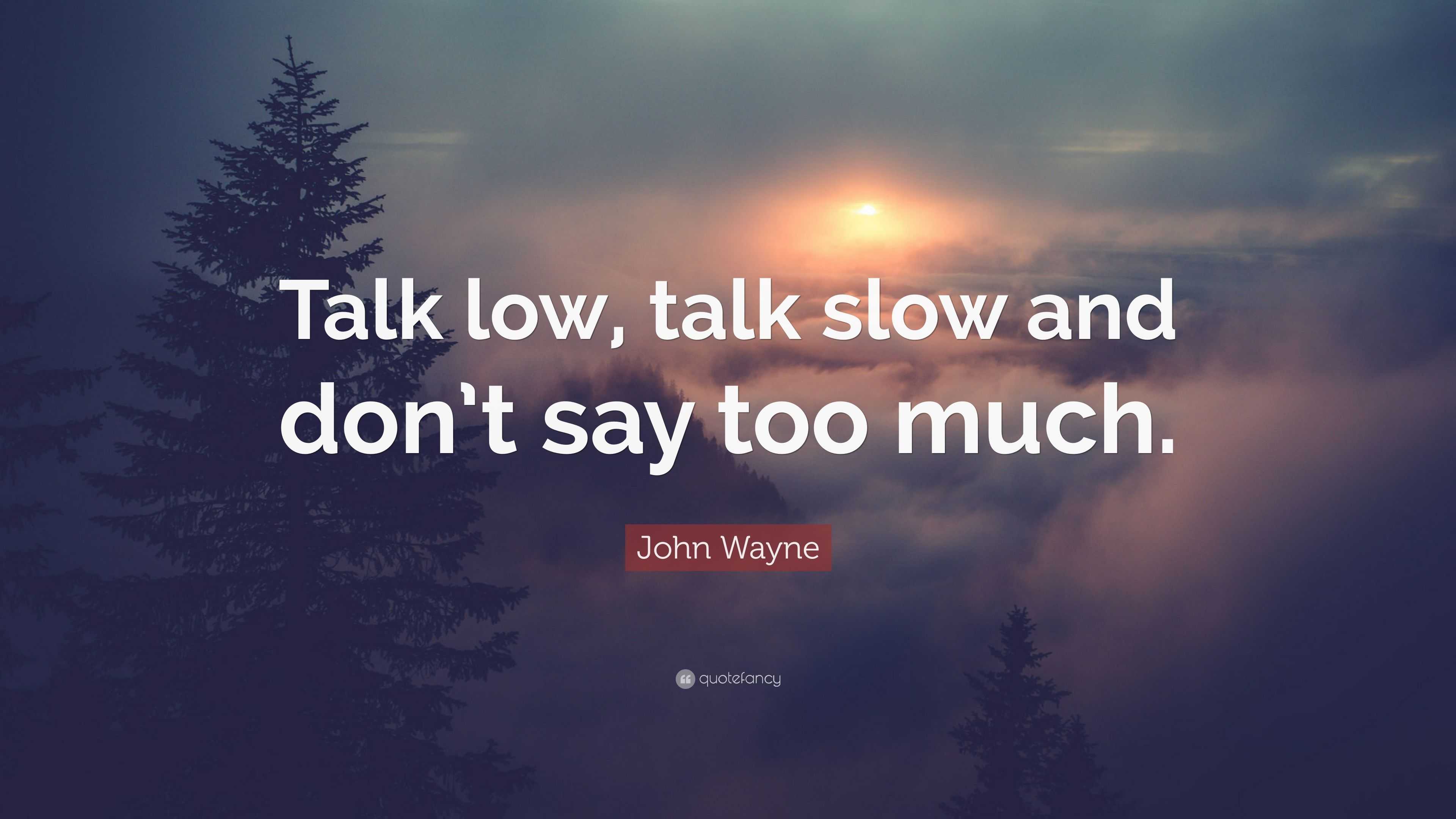
It is obtained from 99Mo ( t 1/2 = 65.94 h), which in turn is obtained from the fission products of natural or reactor uranium, or else by neutron irradiation of 98Mo.Īlthough details vary considerably, the 99Mo is typically incorporated in a “generator” in the form of MoO 4 2− absorbed on a substrate such as alumina where it decays according to the scheme:ĩ9 M o O 4 2 − → β 99 m T c O 4 − → γ 99 T c O 4 − Its properties are ideal for this purpose: it decays into 99Tc by internal transition and γ-emission of sufficient energy to allow the use of physiologically insignificant quantities (nmol or even pmol - a permissible dose of 1 mCi corresponds to 1.92 pmol of 99mTc) and a half-life (6.01 h) short enough to preclude radiological damage due to prolonged exposure. It is injected into the patient in the form of a saline solution of a compound, chosen because it will be absorbed by the organ under investigation, which can then be “imaged” by an X-ray camera or scanner. Technetium in Diagnostic Nuclear Medicine (2)ĩ9mTc is one of the most widely used isotopes in nuclear medicine. for excavators, dredgers, rail crossings, etc. The hard, non–magnetic Hadfield steel containing about 13% Mn and 1.25% C, is the best known, and is used when resistance to severe mechanical shock and wear is required, e.g. Secondly, the presence of Mn as an alloying metal increases the hardness of the steel.
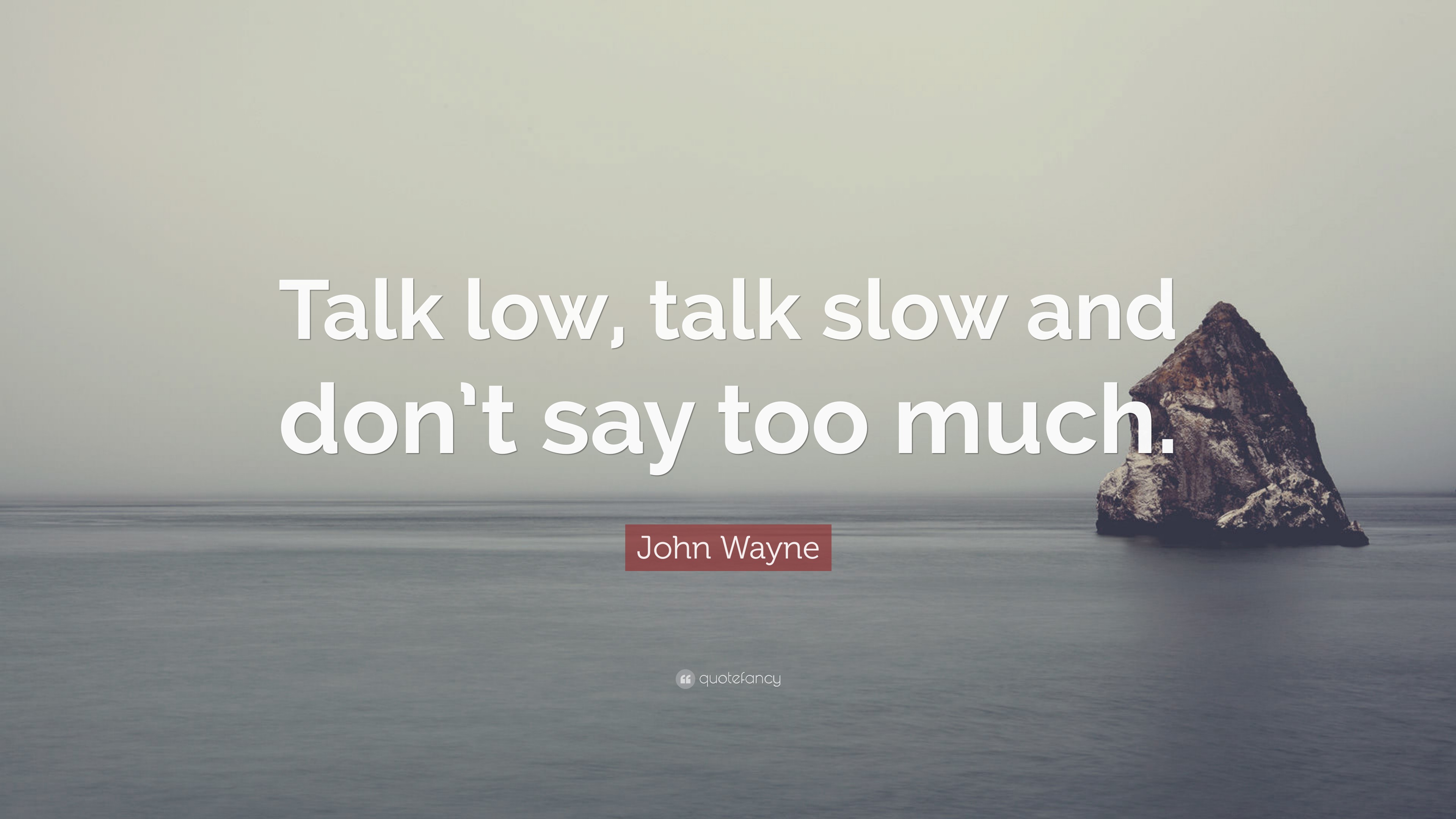
As a “scavenger” it combines with sulfur to form MnS which passes into the slag and prevents the formation of FeS which would induce brittleness, and it also combines with oxygen to form MnO, so preventing the formation of bubbles and pinholes in the cold steel. Mushet ensured the success of the Bessemer process. Ore with an Mn content of over 8 million tonnes was produced in 1995, the most important sources being the former Soviet Union, the Republic of South Africa, Gabon and Australia.Īll steels contain some Mn, and its addition in 1856 by R. Where pure manganese metal is required it is prepared by the electrolysis of aqueous managanese(II) sulfate. Where the Mn content is lower (because of the particular ores used) the product is known as silicomanganese (65–70% Mn, 15–20% Si) or spiegeleisen (5–20% Mn). Dolomite or limestone is also added to remove silica as a slag. (1) This contains about 80% Mn and is made by reducing appropriate amounts of MnO 2 and Fe 2O 3 with coke in a blast furnace or, if cheap electricity is available, in an electric-arc furnace. Over ninety per cent of all the manganese ores produced are used in steel manufacture, mostly in the form of ferromanganese. In Chemistry of the Elements (Second Edition), 1997 24.2.2 Preparation and uses of the metals
